Реферат: Технологические требования к конструкции штампованных деталей (часть 2)
Вырубка наружного контура размером L-D:
Lм = ( L - D)+dм; Lп = ( L - D - Z)-dп, (3. 54), (3. 55)
где dм – допуск на изготовление матрицы, dм = 0,12 ([1], стр. 409, табл. 194);
dп - допуск на изготовление пуансона, dп = 0,06 ([1], стр. 409, табл. 194);
Z – величина двустороннего зазора, Z = 0,8 мм;
D - допуск на изготовление размера, D = 0,6 мм
Для размера 347-0,6:
Lм = (347 – 0,6)+0,12 = 209,5+0,12 мм,
Lп = (347 – 0,6 – 0,8)-0,06 = 208,7-0,06 мм
Остальные элементы контура вычисляются аналогично.
3.4.5.2. Штамп для вырубки.
Расчет толщины и ширины матрицы ([1], стр. 407):
Наименьшая толщина вырубной матрицы:
Н = ( 0,15 ¸ 0,22 ) b, (3. 56)
где b – ширина детали
Н = ( 0,15 ¸ 0,22 ) 347 = 52,05 ¸ 76,34 мм
Наименьшая ширина вырубной матрицы:
В = b + ( 3 ¸ 4) Hmin = 347 + ( 3 ¸ 4 ) 52 = 503 ¸ 555 мм. (3. 57)
3.5. Деталь «Скоба».
Деталь типа Скоба изготовляется из материала
![]() |
лист
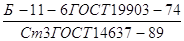
рис. 3.16. Эскиз детали.
3.5.1. Анализ технологичности формы и конструктивных элементов детали. ([1], стр. 280-281)
1. Необходимо избегать сложных конфигураций с узкими и сложными вырезами контура b > 2S = b > 12 мм.
2. Сопряжение в углах внутреннего контура следует выполнять с радиусом закругления r ³ 0,5 S = 3 мм.
3. Радиус гибки должен быть не менее толщины, то-есть 6 мм.
4. Наименьшая высота отгибаемой полки должен быть h ³ 3 S = 18 мм.
5. Линию изгиба желательно располагать поперек линии проката.
Исходя из изложенных ранее технологических требований делаем вывод, что деталь технологична и ее изготовление возможно путем холодной штамповки.
3.5.2. Определение формы и размеров заготовки. Расход материала. ([1], стр. 284)
Для определения ширины полосы и шага вырубки необходимо определить наименьшую величину перемычек ([1], стр. 292, табл. 139), при S = 6 мм, а = b = 3,5 мм.
Развертка детали ([1], стр. 63, табл. 21):
L = 2 ´ l + p ( r + x S ), (3. 58)
где х – коэффициент, х = 0,48
L = 2 ´ 76 + p ( 40 + 0,48 ´ 6 ) = 286,64 мм
Таким образом определяем величину развертки 287-1 мм.
Исходя из этого ширина полосы определяется по формуле ([1], стр.296):
В = L + 2 (b + Dш) + Z, (3. 59)
где Dш – односторонний допуск на ширину полосы ([1], стр. 297, табл. 144), Dш = 3 мм;
Z – гарантийный зазор между направляющими и наибольшей возможной шириной полосы ([1], стр. 297, табл. 143), Z = 1,5 мм
В = 287 + 2 ( 3,5 + 3 ) + 1,5 = 302,5 мм
рис. 3.17. Раскрой полосы.
Выбираем полосу шириной 302,5-1 мм.
Оценку экономичности производим посредством коэффициента раскроя ([1], стр. 287):
кр = (f n / B h) 100%, (3. 60)
где f – площадь поверхности детали,
Для определения площади поверхности детали разобьем ее на элементарные части: f = F1 + 2F2 + 2F3 = 30 ´ 287 + 2 [ ( 17 ´ 43 ) / 2 + 17 ´ 5 ] + 2 [( 51 ´ 43 ) / 2 + 51 ´ 5] = 12214 мм2,
h – шаг вырубки, h = 98 + 3,5 = 101,5 мм,
В – ширина полосы, В = 302,5 мм,
n – количество рядов, n = 1
кр = ( 12214 ´ 1 / 302,5 ´ 101,5) 100% = 39,7%
Величина полезного использования металла определяется общим коэффициентом использования ([1], стр. 290) по формуле:
ки
= , (3.
61)
где m – количество деталей, полученных из листа,
A ´ C – размеры листа, A ´ C = 1500 ´ 3000 мм
рис. 3.18. Раскрой листа.
Из листа получаем 9 полос, из полосы получаем 14 заготовок.
m = 9 ´ 14 = 126 заготовки.
ки
= = 34,2%
Используем другой раскрой полосы, представленный на листе МТ6127.06.001.00. При таком раскрое ширина полосы с учетом а = b= 5 мм.
Выбираем полосу шириной 306-1 мм.
Оценку экономичности производим посредством коэффициента раскроя ([1], стр. 287):
кр = (f n / B h) 100%, (3. 62)
где f – площадь поверхности детали, для определения площади поверхности детали разобьем ее на элементарные части:
f = F1 + 2F2 + 2F3 = 30 ´ 287 + 2 [ ( 17 ´ 43 ) / 2 + 17 ´ 5 ] + 2 [( 51 ´ 43 ) / 2 + 51 ´ 5] = 12214 мм2;
h – шаг вырубки, h = 176 мм;
В – ширина полосы, В = 306 мм;
n – количество рядов, n = 2
кр = ( 12214 ´ 2 / 306 ´ 176) 100% = 45,3 %
Тогда оценку экономичности производим общим коэффициентом использования:
ки
= ,
(3. 63)
Из листа получаем 9 полос, из полросы 17 заготовок.
m = 9 ´ 17 = 153 заготовки
ки
= = 41,53 %
Выбираем данный раскрой материала.
Концевые отходы (полоса шириной 246 мм) используются для изготовления деталей в цехах средней штамповки.
3.5.3 Разработка технологического процесса.
Технологический процесс:
1. Резка листа на полосы и на карточки. Ножницы гильотинные.
2. Штамповка. Вырубка.
3. Механическая обработка отверстия диаметром 4 мм.
4. Штамповка. Гибка.
3.5.4. Выбор оборудования. Расчет усилия пресса.
3.5.4.1.Усилие процесса среза (вырубки).
Расчетное усилие процесса среза штамповки с параллельными режущими кромки определяется по формуле ([1], стр. 16):
Рср = L S sср, (3. 64)
где sср – сопротивление срезу, sср = 45 кг / мм2;
S – толщина детали, S = 6 мм;
L –
периметр среза, L = S l = 2 ´ 98 + 2 +2
+ 4 ´ 5 + 191 ´
2 = 823,9 мм
Рср = 823,9 ´ 6 ´ 45 = 222453 кгс
Полное усилие вырубки составляет:
Р = 1,2 Рср = 1,2 ´ 222453 = 266943,6 кгс (3. 65)
Исходя из конструктивных особенностей пресса, величины хода штампа, выбираем пресс усилием 400 т. с.
3.5.4.2. Усилие гибки.
Расчет усилия гибки:
Так как калибровка, производимая при штамповке, превышает усилие гибки, то рассчитываем максимальное усилие пресса будет при калибровке, то есть
Р = р F, (3. 66)
где р – давление калибровки, р = 8 кгс/мм2 ([1], стр. 73, табл. 26);
F – площадь калибруемой заготовки, F = 191 ´ 30 = 5730 мм2
Р = 8 ´ 5730 = 45840 кгс
Исходя из конструктивных особенностей пресса, закрытой высоты штампа, величины хода пресса, размеров рабочего стола, выбираем пресс усилием 63 т.с. (гидравлический).
Штамп устанавливается на 63 т. с. пресс модели КД2128 – пресс одно-кривошипный открытый двухстоячный простого действия не наклоняемый:
Номинальное усилие на внутреннем ползуне пресса, кН | 630 |
Ход ползуна, мм | 10…100 |
Число ходов в минуту | 125 |
Число одиночных ходов в минуту | 45 |
Мощность электродвигателя 4АС132М6, кВт | 6,3 |
Габаритные размеры, мм 1500 ´ 1690 ´ 2890 |
3.5.5. Конструирование штампов.
3.5.5.1. Штамп для вырубки.
Расчет исполнительных размеров рабочих частей пуансона и матрицы штампа ([1], стр. 407):
Вырубка наружного контура размером D-D:
Dм = ( D - D)+dм; Dп = ( D - D - Z)-dп, (3. 67), (3. 68)
Страницы: 1, 2, 3, 4, 5, 6, 7, 8, 9, 10, 11, 12